Aerospace and Aircraft Components
- Home
- Industries
- Aerospace and Aircraft Components
How Hudson Supports Aerospace Manufacturing
The aerospace industry supplies parts and products to five key market sectors: commercial airlines, general aviation, military aircraft, missiles, and space research. As the components supplied often find application in critical operations where failure is not an option, it is essential they feature high precision, accuracy, durability, and reliability to ensure they function as intended. In the United States, companies that make use of aerospace hardware keep these and other considerations in mind when searching for a manufacturing partner. In particular, one quality they seek is domestic production.
Hudson Technologies is a US-based manufacturer specializing in deep-drawn metal stampings. With nearly eight decades of industry experience, our team has the expertise to accommodate both standard and custom part requests. We are well-versed in meeting exact and tight tolerances for critical applications, making us the ideal partner for all stamped aerospace component needs.
Manufacturing Considerations for Aerospace Components: Industry Regulations and Performance Requirements
When intended for use in the aerospace industry, metal stampings must comply with rigorous quality control and safety standards to prevent injury to operators and damage to equipment. Some of the guidelines concerning aerospace stampings include:
- They must satisfy AS9100 (i.e., the quality standard pertaining to the aerospace industry).
- They must be designed and manufactured to the tightest tolerances possible.
- They must withstand extreme conditions—including high and fluctuating temperatures and pressures—and rigorous testing.
- They must be optimized in regard to strength-to-weight ratio to reduce aircraft weight and, therefore, fuel costs.
- They must include ongoing documentation to facilitate future production line optimization operations (as per national and international industry regulation standards).
Aerospace Component Manufacturing Considerations
Aerospace systems and components require an array of materials and equipment from a variety of manufacturers to produce one aircraft. Hudson Technologies is a leading provider of quality components for commercial, government, and defense aerospace equipment. Using state-of-the-art fabrication technology, we create specialized and custom aerospace components adhering to the most stringent industry guidelines to ensure the utmost reliability for critical no-fail applications. We leverage our expertise to manufacture a variety of components, including:
- Hydraulics for doors, flight controls, thrust reversers, brakes, flaps, and landing gear.
- Valves designed to endure harsh operation conditions typically found in engines and pressurization systems.
- Sensors for flight control, cabin pressure, temperature monitoring, hydraulics, braking, and actuation.
- Diaphragms for cabin environmental control, hydraulic systems, fuel injection, and pressure sensing applications in aqueous environments.
- Lighting Housings used to reliably secure and protect interior and exterior lights.
- Actuators to create motion for engine speed control, braking systems, landing gear, lever control, bay doors, and more.
- Engine Controls allow the pilot to monitor and control aircraft engine operation and protect engine components from damage.
- Antennas for use in communication, navigation, and instrumentation systems.
Hudson Aerospace Components
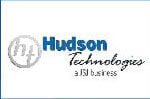
Hudson Aerospace Components
Hover over a point of interest or select a label for more information.
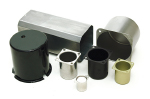
Overall
From actuators to sensors, all aerospace components must be manufactured to tight tolerances to ensure the proper operation of critical systems. As these parts make a significant difference in whether a flight ends successfully or catastrophically, it’s important to understand their function within an aircraft. For more information about a specific component, hover over a point of interest or select a label.
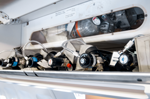
Oxygen Generating Systems
Altogether, onboard oxygen generating parts and components produce and regulate the flow of oxygenated air throughout the aircraft. For aerospace and aviation applications, these systems are particularly critical as personnel and passengers are frequently exposed to low-oxygen environments.
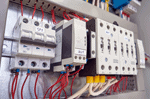
Relays/Switches
In aircraft, relays and switches play a critical role in electrical power supply and distribution systems as they control the input of electricity to various connected devices and systems, allowing them to turn on and off as needed. These components are available in a wide range of designs depending on the specific demands of the aircraft, including electromechanical, solid-state, high-voltage, and time delay.
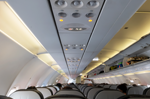
Lighting
Aerospace lighting components find application in both the interior and exterior. Exterior lighting—such as anti-collision and navigation lights—facilitates better visibility (both for the aircraft in question and other aircraft) and is made from durable components designed to withstand harsh environmental conditions, including low and high temperatures, EMI, and extreme vibrations. Interior lighting enhances the comfort levels of passengers and aircraft personnel, allowing them to see within the cockpit and cabin.
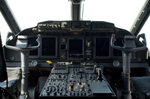
Instrumentation
Aircraft instrument parts typically refer to the devices within the cockpit that facilitate safe and smooth operation. Common instrumentation found in aircraft includes flight instruments (such as altimeters, compasses, and gyroscopes), engine gauges (such as fuel pressure and level sensors), and cluster gauges.
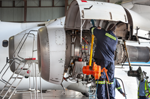
Engine Controls
Aircraft engine controls and monitoring systems protect sensitive engine components from damage and ensure the engine is running at peak performance. These devices often use sensors to take in data about the engine, allowing pilots to adjust operations for better efficiency and facilitating maintenance and diagnostics procedures.
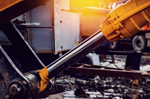
Actuators
In aircraft, actuators convert fluid pressure (hydraulic actuators) or electricity (electric actuators) into linear or rotary motion. This motion drives the operation of several essential aircraft components, such as the landing gear, wing flaps, or bay doors.
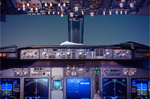
Flight Control Systems
Flight control systems are the primary means by which a pilot manages the direction of travel and altitude of an aircraft. The components of these systems are largely mechanical, with more heavy-duty parts employing hydraulic principles and advanced parts using electronics and fiber optics. Primary flight controls include elevators, stabilizers, and rudders, while secondary flight controls include flaps, slats, and spoilers.
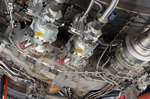
Fuel Systems
Aircraft fuel systems store and distribute the fuel necessary for the flight. They generally consist of tanks, pipes, pumps, filters, valves, and gauges, all of which work together to deliver the fuel to the engine. Depending on the needs of the aircraft, the systems can feature either a gravity feed or pump feed design.
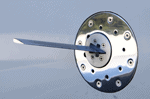
Sensors
Aircraft sensors find application in many aircraft systems. There are several types of sensors available suitable for use in varying applications, including pressure sensors, temperature sensors, position sensors, humidity sensors, and force sensors.
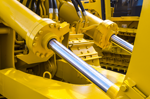
Hydraulics
Hydraulics play a critical role in aircraft ranging from light, single-person planes to large commercial airliners. Depending on the aircraft in question, hydraulic assemblies can be used in the operation of brake systems, steering systems, cargo and loading doors, and more.
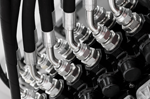
Pressurization Systems
Aircraft pressurization systems maintain interior cabin pressures to facilitate comfortable breathing conditions for passengers and personnel at higher altitudes. Using outflow valves and compressors, they pump in fresh air and pump out spent air, while maintaining cabin pressures of between 11 to 12 psi.
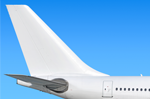
Antennas
Aviation and aerospace antennas are essential components of modern aircraft communication, navigation, and detection systems. Using radio frequency, they serve as a reliable method of sending and receiving important data.
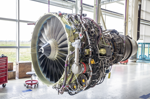
Pressure Valves
Aircraft valves most commonly find use in engines or pressurization systems. Due to their critical function, they must be designed and built to withstand harsh operating conditions, including low pressures, low and high temperatures, and corrosive elements.
Manufacturing Used for Aerospace and Aircraft Components
At Hudson, we know that aerospace components require the highest degree of quality and accuracy. As industry-leading aerospace component manufacturers, we use a variety of manufacturing techniques to create superior aerospace components for highly regulated aerospace and military applications. Our aerospace manufacturing capabilities include:
Custom Design, Engineering, and Tooling
Our experienced team of aerospace parts manufacturers will design, engineer, and manufacture your components from beginning to end, with state-of-the-art CAD technology, prototyping, testing, and custom fabrication. We offer a full catalog of more than 15,000 standardized tools, as well as modification and diaphragm tooling for our customers in the aerospace industry.
Deep-Drawn Stamping
Hudson’s deep-drawn stamping processes can quickly, accurately, and consistently produce large quantities of components by punching sheet metal into a die creating an exceptionally strong, three-dimensional shape with extremely tight tolerances. Our quality deep-drawn stampings are incorporated into a variety of aerospace equipment, including environmental control, flight instrumentation, housings and enclosures, and electrical relays and switches.
Heat Treating and Annealing
Our annealing and heat-treating processes are used to enhance the mechanical properties of certain metals to ensure optimal component performance while maintaining the integrity of their physical characteristics. Heat treatments can be used to strengthen materials by modifying the crystalline structure. Annealing is a specific heat treatment process that makes hard metals less brittle and more ductile for enhanced workability.
CNC Machining and Finishing
Our CNC machining process is accurate and computer-controlled for fast, precise component production. By using this highly automated process, we can create detailed components or add finishing touches to deep-drawn stampings to create flawless mechanical components for a variety of aerospace applications.
Deep Drawn Aerospace Component Specifications, Materials, and Tolerances
With decades of experience, Hudson Technologies offers aerospace sheet metal parts and components in a range of metals, including stainless steel, copper, Am350, and titanium. Our deep drawing capabilities include:
- Size: We can produce aerospace components with diameters between 1/8″ and 12″, and lengths up to 12″. Our corrugated and flat metal diaphragms feature diameters between .200″ and 18″.
- Shape: We are capable of manufacturing aerospace components in a variety of custom shapes, including square, rectangular, round, and asymmetrical.
- Thickness: Our metal component thicknesses range from .002″ to .187″, and our flat and corrugated metal diaphragms are available in thicknesses between .0005″ and .001″.
- Volume: We manufacture components for any scope of work, from single prototypes up to full-scale productions of 5,000,000 products.
- Precision: We maintain exceptionally tight tolerances on custom cases as low as +/- .002″. Tolerances for precision headers are +/- .0005″, and drawn corner radius tolerances are as low as .005″.
Metal aerospace components must be lightweight, strong, and able to withstand extreme environmental stresses. Hudson Technologies offers a variety of versatile materials including:
- Graphene: A stiff material composed of a single layer of graphite that is characterized by high heat resistance and impermeability to gases.
- Fiber-reinforced Composite: Engineered materials that possess high strength and resistance to oxidation at high temperatures.
- Polymer-reinforced Composite: Filler-reinforced polymers that are characterized by their light weight, strength, and heat-resistant properties.
- Glass Fiber: Composites with polymeric structures reinforced by thin glass fibers. They are suitable for aerospace applications due to their low density and high strength.
In addition to our deep drawing techniques, we use heat treatment and annealing processes to enhance the strength and durability of aerospace components.
Industrial Components from Hudson Technologies
Hudson Technologies is proud to be one of the premier aerospace parts suppliers in the industry. We are AS9100D certified, ensuring that every component is manufactured to meet the rigorous requirements of the aerospace and defense industries.
To learn more about our aerospace manufacturing capabilities, visit our Capabilities page or complete a Contact Request.
- They must be designed and manufactured to the tightest tolerances possible.
- They must withstand extreme conditions—including high and fluctuating temperatures and pressures—and rigorous testing.
- They must be optimized in regard to strength-to-weight ratio to reduce aircraft weight and, therefore, fuel costs.
- They must include ongoing documentation to facilitate future production line optimization operations (as per national and international industry regulation standards).
Typical Metal Stamped Aerospace Parts and Components
The metal stamping process produces strong and durable components suitable for use in nearly all areas of aerospace vehicles. Some of the typical aerospace parts and products manufactured include airframes, fasteners and hardware, and various system components.
Aerospace Stamping Capabilities from Hudson Technologies
At Hudson Technologies, we employ metal stamping to produce a wide range of parts and products for use in aerospace and defense applications. The process enables us to create precise three-dimensional shapes from flat sheet metal at a competitive price, especially in large volumes.
We maintain the tooling for over 15,000 standard stamping designs in various shapes and sizes, as well as an in-house design and tooling facility to accommodate custom stampings. Depending on the needs of the customer, we employ one of a broad selection of high-performance metals, including:
- Aluminum
- AHy Mu 80
- Brass
- Nickel
- Cold rolled steel
- Stainless steel
- Copper
- Titanium
- Cupro nickel
Within the aerospace sector, our metal stampings are often used in the following equipment:
- Instrumentation
- Oxygen generating systems
- Military aircraft housings and enclosures
- Relays, switches and lighting systems
Why Partner with Hudson Technologies?
By choosing us as their source for aerospace components, our customers benefit from our industry experience, product selection and eco-friendliness.
In addition to aerospace applications, our stampings play an integral role in many other industrial applications, including the following:
- Automotive
- Aviation
- Commercial battery
- Edge welded bellows
- Electrical
- Flowmeters
- Implantable medical devices
- Irrigation
- Mechanical seals
- Metal diaphragms
- Relay cases
- Semiconductor