Hudson Technologies produces deep drawn metal battery enclosures for a variety of industries, including energy storage. In recent years, we’ve worked to provide innovative solutions to any company working to store energy from intermittent or renewable sources such as wind and solar power.
Industry Challenges
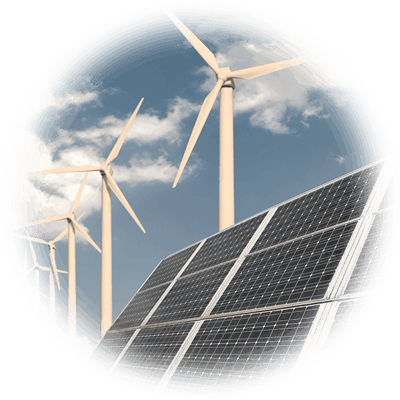
The rise of renewable energy has spurred a significant increase in the demand for energy storage. However, energy storage providers currently confront many challenges, including:
- The limited commercialization potential of many energy storage technologies
- The failure of standard power system models to capture the value proposition of energy storage
- The inability of existing systems to communicate and control energy storage
In terms of battery technology, much remains to be done to improve the limited cycling times of batteries, which are primarily caused by electrode fouling and electrolyte degradation. A possible solution to this issue is the use of electrochemical energy storage technologies that convert electricity into chemical potential for storage before reconverting it into electricity prior to loading.